Tugger trains from every angle – an expert’s opinion
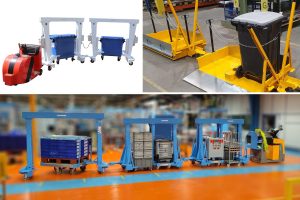
Tugger trains offer a novel and efficient approach to supply chain and production management for industry. Inspired by the principles of the Toyota Production System (TPS) and Lean Manufacturing, the concept aims to streamline operations by reducing stocks to an absolute minimum while meeting production requirements in a precise and responsive manner. Tugger train implementation requires a top-quality provider with the ability to adapt to client needs. Later on we provide a few examples of tugger train systems designed to optimise line-side supply for any business sector.
Tugger train: the concept explained down to the minutest detail
What is a tugger train?
A tugger train – also known as a “tugger cart system”, “LEAN manufacturing train” or “milk-run train” – refers to a supply chain and production management approach based on the Just-In-Time principle. The aim is to minimise stock levels by supplying raw materials, components and semi-finished products at the precise moment when they are needed for production.
This approach is based on precise synchronisation between demand and supply, in a bid to eliminate waste, improve efficiency and maintain a continuous flow of parts necessary for production, all the while avoiding delays and needless stoppages.
A tugger train has the following technical parts:
- At the front there is a tractor: manual, semi-automatic or automatic;
- This is followed by wagons – also known as mother carts or sulkies. The number of wagons defines the train length. There are gantries that can be used to remove and insert trolleys either side of the train to improve productivity;
- Trolleys – also known as daughter carts or dollies – can be inserted or removed from the wagons in any order. Along the route of the tugger train, the operator can swap an empty trolley for a full one (or vice versa). Depending on the existing models, the wagons can accommodate trolleys of different sizes: 600×400, 800×600, 1200×800, 1000x1200mm, etc.
In short, the single-track train system optimises line-side supply. Flows are maximised thanks to one train journey and a quick and easy swap between a full and an empty trolley directly at the workstation.
How did tugger trains materialise?
The tugger train concept originated from the production management system developed by Toyota after the Second World War: the Toyota Production System (TPS). It is based on principles aiming to minimise waste (muda), maximise value for the client and improve processes on a continual basis. The TPS focuses on reducing costs, product quality and production speed by eliminating all forms of waste such as surplus stocks, waiting times and needless movements, etc.
Lean Manufacturing is a management approach broadly inspired by the Toyota Production System. It is a method designed to optimise manufacturing operations by eliminating unnecessary steps in the manufacturing cycle that do not add value to the end product. Lean Manufacturing aims to reduce costs while maintaining quality and meeting client requirements efficiently.
Tugger trains are an extension of the Lean principles applied to the supply chain and logistics. They can optimise transportation of materials and components in a plant or production workshop. They are implemented to minimise wastage of time, space and resources associated with transport, while ensuring a continuous regular flow of materials necessary for production.
Over time, the tugger train concept has spread throughout the industrial world and been adopted by many businesses wishing to improve their operational efficiency and reduce costs related to supply chain management. Consequently, although the roots of this approach can be traced back to the 1950s and 1960s, its application continues to develop and adapt to the changing needs of modern industry.
What are the most fitting business sectors for tugger train implementation?
The concept of tugger trains, also known as “milk-run trains”, is used in various business sectors to optimise supply chain management and reduce costs related to the transport of materials and components. Below are some of the business sectors and common uses of tugger trains:
- Automotive: The automotive industry makes extensive use of tugger trains to deliver components to production lines. Automakers and their suppliers often use optimised itineraries to group together deliveries of parts and maintain a continuous production flow.
- Manufacturing: In various manufacturing industries, tugger trains are used to deliver raw materials, components and semi-finished products efficiently to the different stages in the production process.
- Aeronautical: The aeronautical industry also uses tugger train approaches to ensure timely delivery of complex parts and materials required for aircraft manufacturing.
- Electronics: Companies in the electronics and IT sector use tugger trains to manage electronic component and equipment supplies.
- Pharmaceutical industry: Tugger trains can be used by pharmaceutical manufacturers to transport the raw materials needed to produce medicines and pharmaceuticals.
- Retail: Distribution centres and warehouses may adopt tugger train methods to optimise the receipt, storage and dispatch of goods to points of sale or end customers.
- Food industry: Fresh or perishable foods may also benefit from the tugger train approach to minimise waiting times and ensure fast delivery to points of sale.
- Textiles and apparel: The textile industry may use tugger trains to transport fabrics, materials and clothing between the different stages of the production process.
- Chemical industry: Chemical companies may apply tugger train strategies to manage flows of chemical raw materials and finished products.
To sum up, tugger trains offer a versatile approach that can be adapted to accommodate different business sectors in order to optimise the supply chain, reduce transport costs and improve operational efficiency.
What are the advantages of tugger trains?
The implementation of a tugger train, also referred to as a lean manufacturing approach in logistics management, offers several significant advantages for a production site:
- Reduces storage costs: By adopting a tugger train, stock levels are kept to a minimum, which reduces the costs related to storage and management of surplus stocks.
- Minimises waste: By supplying raw materials and components at the exact time they are needed, tugger trains reduce wastage due to excess production, delays and surpluses.
- Improves response times: The lean approach can be used to quickly respond to variations in demand, by adjusting production to real market requirements.
- Reduces waiting times: Tugger trains eliminate waiting times by supplying the parts needed at the exact time they are required, and this speeds up the production process.
- Improves quality: By avoiding excess production and problems related to long-term storage, tugger trains help to maintain product quality by minimising risks of deterioration or defects.
- Optimises resources: The lean manufacturing approach promotes better use of resources, as raw materials and their components are used as and when received, thus reducing the need for storage space and labour for stock management.
- Identifies problems early: By maintaining a continuous flow of materials and components, production problems and abnormalities can be detected faster, and this facilitates immediate resolution.
- Increases flexibility: Lean manufacturing enables new products to be integrated more easily or changes in demand to be accommodated as the system is designed to be responsive and flexible.
- Simplifies operations: Tugger trains simplify processes by eliminating complex stock management stages, which can reduce administrative workload and operational complexity.
- Improves overall efficiency: By eliminating waste and optimising the supply chain, tugger trains contribute to an overall increase in business efficiency and profitability.
In summary, implementation of tugger trains promotes a more agile, responsive and efficient approach to logistics management, and this can result in significant improvements in production operations.
Design and manufacturing of custom-built tugger trains
Your trusted partner for custom-built tugger trains
Over the years, ManuLine has made a name for itself as a supplier of custom-built internal logistics solutions. The company has extensive experience in the design and manufacture of specific tugger trains.
- Experience and expertise: With two decades of experience in the sector, ManuLine has built up extensive experience in the design and production of custom-built tugger trains. Our long-standing presence on the market bears witness to our reliability and our ability to fulfil our clients’ specific requirements.
- Individualised approach: The ManuLine team places great importance on the specific needs of every company. We work closely with our clients to identify their needs clearly and design a tugger train that is fully customised and perfectly meets their expectations.
- Engineering expertise: ManuLine’s design office has a wealth of expertise in 3D computer-aided design and engineering of tugger trains. We develop innovative, effective technical solutions to ensure the functionality, safety and optimal durability of our trains.
- Outstanding materials and components: At ManuLine, we place great emphasis on the quality of the materials and components used to manufacture our custom-built tugger trains. Our goal is to ensure that our products are robust, ergonomic and long-lasting.
- Flexibility and adaptability: Tugger trains designed by ManuLine can be fully adjusted and customised to meet the particular needs of each client. Our ability to address the requirements of a constantly evolving industrial sector enables us to supply tugger trains that meet the most exacting standards of companies.
- Technical & Sales Department: The ManuLine technical & sales team provides full monitoring of each client project, with a view to all aspects of the specs, from technical dimensions to budget limitations. Whatever the distance, we are willing to travel to meet our clients and offer the best solution.
To sum up, ManuLine stands out as a top-quality supplier when it comes to designing and manufacturing custom-built tugger trains thanks to its engineering expertise, personalised approach, flexibility, client support and the quality of the materials used. We can provide reliable solutions that are tailored to each client’s specific needs.
Examples of our custom-built tugger trains
Below are some examples of tugger trains for optimising line-side supply.
Custom-built tugger train for transporting trolleys of different sizes & loads
Custom-built tugger train designed for a world-leading automotive industry supplier. This flexible solution can transport trolleys measuring 800×600, 600×400 and/or 1200×800 mm. They can be removed and inserted either side of the tugger train in any order and extremely fast.
Custom-built tugger train for transporting bins
Custom-built tugger train designed for a world-leading supplier of measurement instrumentation, services and solutions for industrial processes. It is designed for both indoor and outdoor use. The containers remain raised throughout the tugger train’s entire journey.
Another custom-built tugger train model for transporting bins
Custom-built tugger train for transporting bins measuring 550×580 mm for a world-leading transmission belt supplier. The bins can be inserted and removed either side of the tugger train. Side panels and chains secure the bins during the journey.
Custom-built tugger train for transporting 600x400mm plastic boxes
Custom-built tugger train for an international leader in optical solutions. Each trolley can transport a stack of plastic boxes up to a height of 1,500 mm. A shooter system on the conveyor automatically unlocks the trolley’s retractable latch.
Steps involved in the development of a custom-built tugger train
ManuLine has adopted a comprehensive approach to designing and manufacturing custom-built tugger trains:
- Needs assessment: after initial contact, the ManuLine team and its design office analyse the clients’ specifications taking into account the weight, dimensions, load and working environment requirements as well as the desired features of the custom-built tugger train.
- Technical design: based on the specifications provided, the design office develops a technical concept, which includes the choice of materials, the general tugger train structure, ergonomic characteristics and options, and the safety system.
- Drawings and plans: once the technical design has been approved, drawings and plans are prepared. These items specify the dimensions, materials specifications, assemblies and technical details needed to manufacture the custom-built tugger train.
- Manufacturing: the custom-built tugger train is entirely manufactured by AMS Tôlerie Fine, a company affiliated with the Fidève Group to which ManuLine also belongs. The fully made-in-France tugger train is then produced according to the plans drawn up. The chosen materials are cut, shaped, welded, assembled and finished to create the tugger train structure. Components such as castors, brakes, handles and other components are then added pursuant to the required specifications.
- Quality control: a quality check process is implemented at various production stages to ensure compliance with standards and requirements. This includes resistance tests, measurement checks, visual inspections and other quality assurance procedures.
- Finish and customisation: once the tugger train has been assembled, further adaptations may be made according to the client’s preferences. This may involve the addition of rotating bases, specific attachment devices, protective coatings or other special features.
In sum, ManuLine has implemented a methodical process for designing and manufacturing custom-built tugger trains. The team and design department can incorporate the client’s particular requirements to build a solution that is truly adapted and operational.
You can rely on ManuLine to optimise internal logistics flows
ManuLine’s custom-built intralogistics solutions meet all internal logistics flow project requirements. Do you also need a solution for moving loads/containers within your industrial site? Our design office would be happy to review your specs and work with you to develop the custom-built trolley best tailored to your needs.
Custom-built solutions for transporting loads internally