Case study: custom-built tugger train for transporting 600 x 400-mm plastic boxes
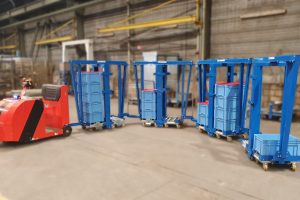
ManuLine is a French company specialising in the design, manufacturing and sale of intralogistics solutions, particularly tugger trains. The products are designed to be used in a flexible and modular production environment, in accordance with the principles of lean manufacturing. Raw materials, semi-finished & finished products and waste are transported quickly and efficiently, while reducing waiting times and wastage. Below is a case study of a ManuLine Client who wished to improve line-side supply of 600 x 400-mm plastic boxes on its industrial site.
Our Client’s intralogistics needs
Our Client is an international leader in optical solutions. Several problems on its industrial site led to the implementation of a tugger train.
- Material flows: A large number of 400 x 600-mm plastic boxes transited through the industrial site each day. They were painstakingly transported and transferred on a conveyor, one by one. The implementation of a tugger train makes it possible to transport several plastic boxes between locations on the site quickly and efficiently.
- Safety: Industrial sites can be dangerous for workers, with moving machinery and heavy equipment. A tugger train with adapted trolleys improves transport ergonomics and makes manual loading and unloading more comfortable for the operator. These improved ergonomics reduce the number of MSDs and drastically alleviate the strain of repetitive tasks.
- Efficiency: Transporting plastic boxes manually is slow and inefficient, especially on large-scale industrial sites. A tugger train helps to optimise and improve flows by reducing masked times and empty forklift returns when transferring or transporting loads.
- Distance: Our Client’s industrial site is spread over large distances, which makes transporting plastic boxes difficult and tiring for workers. A tugger train can transport materials over long distances more quickly and efficiently.
To sum up, a tugger train improves an industrial site’s efficiency, safety and productivity while resolving some of the logistical problems which it may encounter. Implementing a tugger train on our Client’s industrial site helps to improve both the supply loop and the internal logistics.
Constraints regarding the implementation of a tugger train
Several constraints needed to be taken into account when designing a tugger train for our Client’s site. Firstly, the ManuLine team had to adapt to the Client’s existing conveyor system. What’s more, the tugger train had to be able to transfer stacks of 400 x 600-mm plastic boxes in an entirely safe manner.
ManuLine therefore worked jointly with the Client and the conveyor manufacturer. The challenge involved adapting to the existing facilities, and thus adapting to the conveyor height while offering a safe and ergonomic solution for transferring stacks of boxes. ManuLine specially designed a trolley with specific dimensions, which was compatible with the “Crossing Storci” train model.
Custom-built tugger train suggested by ManuLine
What is a tugger train?
A tugger train is a lean manufacturing means of transport which optimises the supply of goods and materials over short distances in a production environment. It is generally designed to adapt to tight workspaces and to different types of containers and materials.
Tugger trains are often used in factories and warehouses which apply the lean manufacturing method, with a view to minimising waste and maximising added value for the Client. They can be used for transporting raw materials, semi-finished or finished products between production areas or for supplying production lines.
To best meet our Client’s requirements, the ManuLine team suggested implementing a “Crossing Storci” tugger train. This tugger train model is ideal for transporting small containers – such as 600 x 400-mm plastic boxes – quickly and efficiently along the production line.
Operation of the custom-built tugger train
The “Crossing Storci” tugger train implemented on our Client’s industrial site can transport trolleys measuring 610 x 410 mm. Each trolley can transport a stack of 600 x 400-mm plastic boxes up to a height of 1,500 mm. These boxes are held on the trolleys by 3 fixed edges and a retractable latch. The “Crossing Storci” tugger train operation stages are as follows:
- First, the operator fills his boxes with parts at the workstation, then he gradually stacks them up on a trolley. This trolley is positioned on an electric lifting device for optimum ergonomics.
- Once a pile of 5 boxes is stacked on the trolley, the operator puts the full trolley on the aisle side.
- When the train arrives, the driver retrieves the full trolley and leaves behind an empty one so that the operator always has a trolley available, thus optimising work time. Thanks to the Crossing Storci’s gantry, trolleys can be exchanged on either side of the train. Trolleys can also be inserted freely in the trains when needed and in any order.
- The train continues its journey from one workstation to the next, and once it arrives at the logistics area, the driver removes the trolleys from the train one by one, then docks at a roller conveyor to transfer the stack of boxes.
- A shooter system on the conveyor automatically unlocks the trolley’s retractable latch. All the operator has to do is push the stack of boxes, which is then carried away on the roller conveyor.
Video: How to use the “Crossing Storci” tugger train
Advantages of the “Crossing Storci” tugger train
This tugger train has many advantages:
- Reduced waiting times: The tugger train transports goods and materials over short distances, which helps to reduce waiting times between the different production stages.
- Greater flexibility: The tugger train can be adapted to different types of containers and materials, offering greater flexibility and a faster adaptation to changes in demand.
- Less waste: By using a tugger train, the company can reduce unnecessary trips and transport times, which helps to reduce waste and minimise costs.
- Optimised space: The single-track tugger train adapts to tight workspaces and narrow aisles, making better use of the available space.
- Reduced costs: By reducing waste and optimising the use of space, the tugger train helps to reduce production costs and improve the company’s profitability.
- Improved safety as there are fewer (or no) forklifts on the production line. Tugger trains can also be equipped with safety devices to prevent accidents and injuries in the production environment.
- Fast operation
- Greater flexibility: Trolleys can be unloaded to the left and/or right of the tugger train.
- Ergonomic and easy to use
- Reduced maintenance thanks to the 100% mechanical operation of the “Crossing Storci” tugger train.
In short, by using the tugger train, the Client can improve its efficiency, productivity and profitability by reducing waste, optimising the use of space and maximising added value.
You can rely on ManuLine to optimise internal logistics flows
ManuLine offers innovative intralogistics solutions which are tailored to companies’ specific needs, with tugger trains designed to be flexible, modular and in line with lean manufacturing principles.
Discover all of our custom-built solutions for transporting loads internally below:
Do you also need a solution for moving loads/containers within your industrial site? Our design office would be happy to review your specs and work with you to develop the tugger train best tailored to your needs.
CONTACT US