Emptying station for plastic injection industry
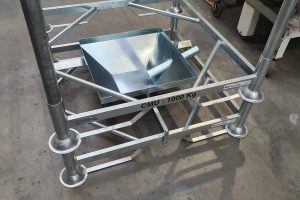
ManuLine is a company located in Alsace with 20 years’ experience as a specialist in bulk handling optimisation solutions. We provide custom-built solutions for Big Bag handling, emptying, filling and storage. For a client in the plastic injection industry, our team recently developed a custom-built station with hopper and sleeve for emptying plastic granules. In this article we review the composition & characteristics of the emptying station, and its operation.
Custom-built emptying station with hopper and sleeve
Why choose an emptying station with hopper and sleeve?
The emptying station is equipped with a hopper to facilitate unloading of Big Bag contents. It has a sleeve to guarantee secure, controlled transfer of contents to plastic injection presses. The customised design solution has enabled the emptying station to be adapted to the specifications and requirements of the process or material used.
What are the technical features of the emptying station?
The emptying station is essential for industrial operations involving efficient transfer of bulk materials. The station was designed to best meet our client’s specs and has the following features:
- The emptying station has a structure with a 1200 mm centre-to-centre distance and a hopper equipped with an outlet to accommodate a sleeve.
- Its galvanised finish prevents corrosion and ensures durability.
- It is specially designed to accommodate Big Bags measuring 1030 mm x 1030 mm and 1600 mm high, with a maximum load capacity of 1 ton.
- The station is suitable for Big Bags using 4 standard corner loops stitched in the vertical seams of the bag.
- With a working height of 250 mm, it provides adequate room for emptying materials.
- The 550 mm diameter and 500 mm high discharge spout facilitates the transfer of plastic granules, characterised by particle sizes of ø 2 to 3 mm.
What is the emptying station with hopper and sleeve made up of?
The emptying station developed for our client features the following elements:
- 1 spreader beam equipped with fork slots, with CMU : 1000 Kg (Safe Working Load: 1000 kg) marked on 2 sides.
- 4 tubes 2400 mm long (that can be cut to size as necessary).
- 1 base frame also marked CMU : 1000 kg on 2 sides.
- 4 x 345 mm tubes high enough to allow the passage of the hopper sleeve.
- 1 electro-galvanised hopper with a flat bottom and outlet equipped with a sleeve of diameter 70 mm (inlet diameter: 64.2 mm).
- 1 supporting base for the hopper.
How does the emptying station with hopper and sleeve work?
The emptying station with hopper and sleeve efficiently transfers the plastic granules from the Big Bags. This is how it works:
- Big Bag handling: To start with, the Big Bag is lifted by its spreader beam with a hoist or stacker. The stacker fork length must be 1150 mm to ensure safe handling. It is important that the bag base does not rest on top of the hopper.
- Emptying station positioning: Once the Big Bag has been lifted it is positioned over the emptying station by the spreader beam or an overhead crane. This guarantees that the bag is correctly aligned for the emptying process.
- Discharge spout unfolding: Once the bag is in place, the discharge spout is unfolded and the bag knot is untied. The Big Bag contents flow into the hopper below.
- Automatic flow control: As soon as the hopper is half full, the flow of plastic granules regulates itself automatically. This is possible due to the precise position of the discharge spout.
- Granule suction: To transfer the plastic granules to their destination, a suction lance is inserted into the hopper sleeve.
- The lance sucks the granules up and transfers them to the pneumatic distribution system. The granules are then transported to the different injection presses to be used in the manufacturing process.
To sum up, the emptying station with hopper and sleeve simplifies the transfer of plastic granules from Big Bags by regulating the flow and ensuring efficient delivery to production equipment. This system helps to improve the efficiency of operations in industries that use these types of bulk materials.
You can rely on ManuLine for your Big Bag emptying requirements
The ManuLine design office develops ergonomic and innovative solutions for emptying your Big Bags in a simple and efficient manner. Our models can be fully customised to best meet individual needs related to the type of materials to be emptied, their particle size, flow control requirements and the specific applications of each client. Here is an idea of our different stations:
- The emptying station with industrial slide gate valve, also known as a knife gate valve, facilitates complete unloading in a single operation and ensures approximate flow control during the emptying process. This option is particularly suited to large particle size materials (>6 mm), such as plastic granules, metals or minerals.
- The emptying station with diaphragm valve is the ideal choice for situations requiring meticulous flow control for materials. It uses a diaphragm to modulate valve opening, thus ensuring unloading with an extremely high degree of precision. In addition, in certain models, Big Bags can be replaced during emptying, and this considerably reduces process downtimes. One example of our designs is the emptying station with electric diaphragm valve for the agri-food sector.
- The emptying station with check valve, sometimes known as a butterfly valve, allows unloading in one go as well as basic flow control during emptying. It is particularly suited to small particle size materials (<6 mm), such as powders and powdery products, and is often useful in sectors such as the chemicals and mineral industries and cement production.
- The emptying station with flat bottom hopper and sleeve is very versatile. It is suited to a wide range of bulk materials in a variety of forms such as granules, powders and powdery products. The flat bottom hopper ensures Big Bag stability, and the sleeve is attached to the transfer system’s suction lance, which provides precise flow control. One example of our work is the emptying station with hopper and sleeve for the automotive sector.
- The emptying station with seed valve has been specially designed for the agricultural sector. Its primary purpose is to ensure controlled discharge of seed, granules or grain from Big Bags. The advantage lies in its ability to precisely control the flow, thus ensuring an even distribution of seed during crop planting operations.