Optimizing Bulk Material Handling: A Case Study on a Custom Big Bag Filling Station
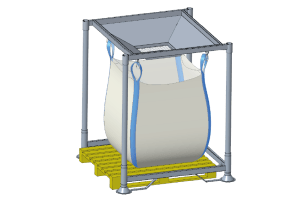
In the industrial sector, handling bulk materials requires specific solutions to ensure safety, efficiency, and ergonomic operations. Each work environment comes with its unique challenges, often necessitating custom equipment to safely meet handling and storage needs.
This article explores how ManuLine addressed the specific needs of an industrial client by designing a custom big bag filling station. With advanced filtration capabilities and a modular design, ManuLine enabled the client to optimize production flows and enhance operator safety. This case study highlights ManuLine’s expertise in tailor-made design while offering insights into complementary solutions and their benefits for the industrial sector.
A Big Bag Filling Station Designed to Meet the Client’s Specific Needs
Analyzing Client Requirements and Specific Challenges
The client, operating in the industrial sector, faced challenges that required a big bag filling solution with precise filtration criteria. The raw material handled contained impurities of varying sizes, such as bag fragments or other debris, necessitating a filtration system that retained only the desired powder particles.
Two main challenges were identified:
- Efficient filtration to ensure the purity of the material stored in the big bags.
- Safety and ergonomics: a structure adapted to operators, facilitating their tasks while reducing the risk of inhaling dust.
Development of a Custom Big Bag Filling Station
To address the client’s requirements, ManuLine designed a tailor-made filling station equipped with several specific features:
- Customized mesh hopper: The hopper was designed with a 30×30 mm mesh, enabling effective filtration that captures large impurities while allowing the powder to pass through. This choice is ideal for industrial environments where product purity is critical, as it blocks larger debris without disrupting the flow of fine material.
- Hook system for big bag positioning: This system keeps the big bag straps open, facilitating filling without the need for continuous manual handling.
- Modular station design: The station was built with modularity in mind, allowing it to integrate seamlessly into the client’s existing production lines. Should production needs evolve, the modular design allows for quick and flexible reconfiguration.
“This solution ensures optimal safety for operators while enhancing the efficiency of big bag filling thanks to an ergonomic and well-thought-out structure,” explains the ManuLine technical team.
Possible Variations for Other Industrial Needs
Beyond this specific solution, ManuLine has developed other variations of filling stations to meet diverse needs in various industries:
- Filling station with spout and covered hopper: Ideal for fine materials, this station includes a covered hopper that reduces dust emissions and ensures controlled material flow, preventing overflows.
- Station with filtration rods and roofed hopper: Designed for materials containing larger impurities, this station features filtration rods that retain debris. The hopper roof channels the material, ensuring maximum safety during filling operations.
The Benefits of a Custom Big Bag Filling Station in the Industrial Sector
Enhancing Safety and Ergonomics for the Client
ManuLine’s tailor-made solutions meet the highest safety standards, minimizing risks for operators:
- Enhanced safety: With covered hoppers and filtration systems, dust emissions are controlled, ensuring better air quality in the workspace. Large debris is captured upstream, guaranteeing a pure finished product.
- Optimized ergonomics: The station’s modularity allows operators to work in comfortable positions, reducing fatigue from repetitive tasks. Adjustable stations facilitate big bag filling while minimizing unnecessary movements, helping to prevent musculoskeletal disorders (MSDs), a critical issue in industrial environments with frequent manual handling of heavy loads.
Economic and Production Flow Optimization
A custom big bag filling station also offers significant economic benefits:
- Reduced operating costs: Improved station efficiency decreases the time operators spend on each task, lowering labor costs.
- Minimized material waste: Filtration and controlled filling systems limit raw material waste, maximizing resource utilization.
- Increased productivity: Fewer machine adjustments and quick, secure big bag integration accelerate processing speeds. This enhanced productivity allows for higher throughput without additional resources.
Environmental Contribution Through Advanced Filling and Filtration Solutions
ManuLine’s big bag filling station also delivers environmental benefits by reducing dust emissions and material waste. By controlling losses and ensuring strict material management, this solution helps limit the environmental impact of its users. With integrated filtration systems and waste reduction features, ManuLine meets the growing demand for sustainability in the industrial sector, where reducing the ecological footprint is becoming a priority.
Complementary Equipment for Optimized Bulk Material Handling
In addition to filling stations, ManuLine offers complementary solutions for comprehensive bulk material management:
- Discharge stations: These stations enable easy unloading of big bag contents, ensuring controlled material flow and enhanced operator safety during discharge operations.
- Manubag: A storage support system for big bags that optimizes warehouse space management. It ensures secure stacking to maximize storage capacity while maintaining stability.
These complementary solutions provide a fully integrated approach to bulk material handling, optimizing industrial processes and ensuring continuous safety for teams.
Conclusion: ManuLine’s Expertise and the Value of a Custom Solution
This case study demonstrates ManuLine’s expertise in designing big bag filling solutions tailored to the precise needs of industrial clients. By addressing filtration, ergonomic, and safety requirements, ManuLine helps clients optimize processes, reduce operational costs, and improve working conditions for their operators.
With modular solutions and complementary equipment such as discharge stations and the Manubag, ManuLine positions itself as a trusted partner for any company seeking to optimize bulk material handling. Through custom solutions, ManuLine enables businesses to achieve their production goals while ensuring a safe and efficient working environment.
Discover ManuLine’s tailored solutions for optimizing bulk material handling
Glossary of Technical Terms
- Hopper: A funnel-shaped container used to store and distribute bulk materials.
- Modularity: The ability of equipment to be configured or adjusted to specific or changing needs.
- Material filtration: A process that separates unwanted materials or impurities from the primary material flow to produce a purified product.